Sistemas de bombeo: Larga vida a la operación
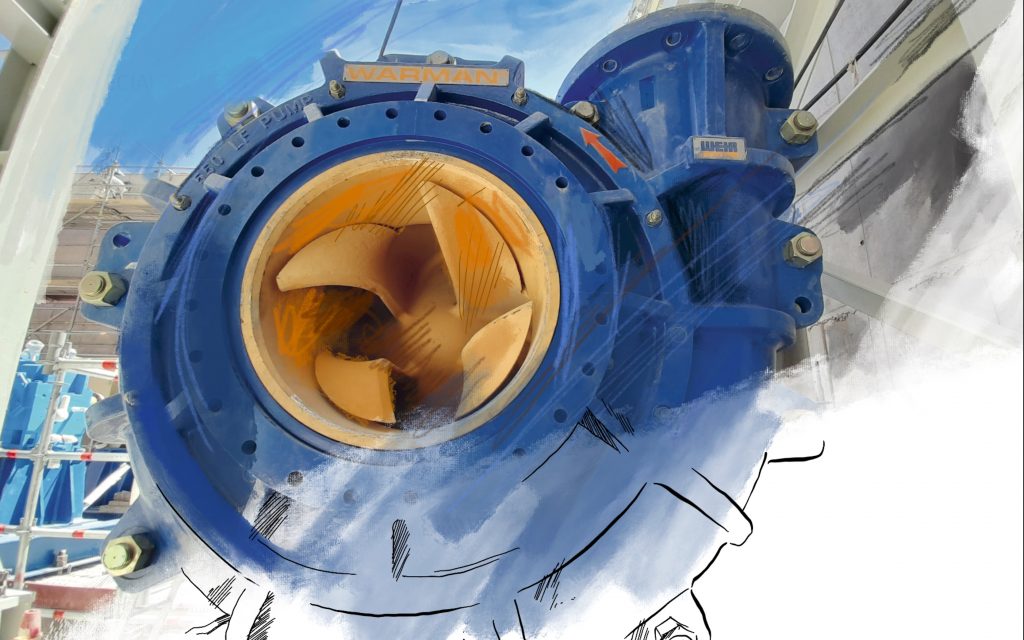
¿Quién dijo que las bombas tienen una corta vida útil?, gracias a sofisticados modelos tecnológicos, sumado a asesorías en el punto de operación, hoy la industria brinda mucha más durabilidad entregando valiosos ahorros.
Por Marina Parisi
___________________________
Aburrida de tratar de optimizar su proceso de tratamiento de relaves, una importante empresa minera estaba a punto de arrojar la toalla.
“La faena tenía un sistema tradicional compuesto por tranques de relaves, los que cada día presentan más restricciones medioambientales, debido a los peligros de derrumbe, además de todo el impacto en la naturaleza y en las comunidades cercanas”, asevera Héctor Avendaño, gerente técnico de Eral Chile. “Por ello diseñamos e implementamos una solución a la medida llamada “Tratamiento No Convencional de Relaves mediante Hidro-Escurrido”.
La iniciativa incluye una cuba de recepción de pulpa y dos grupos motor-bomba, de tal forma que esta arquitectura impulsa la pulpa hacia la batería secundaria de relaves, describe el ejecutivo. “Asimismo, incorpora bombas centrífugas horizontales modelo 12/10, con revestimientos internos en acero de alto cromo, adecuados para minimizar el desgaste por abrasión”.
Adicionalmente, se integró un sistema mata presión a la cuba de impulsión, que evita el desgaste por abrasión propio del fluido y aumenta la vida útil de todo el conjunto. “De esta forma, se incrementa la durabilidad de la operación en régimen, minimizando paradas por concepto de reparaciones”, grafica Avendaño.
¿Resultado?, con la puesta en marcha del nuevo proyecto, el 70% del relave es procesado en forma sólida-seca, “eliminando el tranque de relaves, aliviando la operación de los tanques espesadores-clarificadores y optimizando todo el proceso de recuperación de agua”, recalca el ejecutivo. “Toda esta operación resulta mucho más efectiva y segura para el ecosistema”.
Otro dato importante: la solución logró superar el 96% de disponibilidad del sistema, en circunstancias que la antigua arquitectura solo alcanzaba el 80% de disponibilidad, precisa Avendaño. “Por último, este sistema recupera el agua del proceso en la planta disminuyendo el costo del transporte de agua de reposición, lo que resulta crítico considerando que el acceso a agua fresca ya no es factible para la minería”.
Un tema de gestión
Mientras tanto, en el Norte Grande de Chile otro productor de minerales entusiasmado abrazó el objetivo de inaugurar una nueva planta concentradora y en un breve lapso de tiempo. Este complejo incluía gran cantidad de equipos de impulsión que estarían ubicados en diferentes puntos estratégicos de la faena.
La implementación del nuevo proyecto arrancó bien, hasta que los equipos de bombeo comenzaron a retrasarse desde la fábrica y no llegaban a la hora acordada, explica Cristian Toro, leader pump Sales Metso Outotec. “Esto generó una enorme presión sobre nosotros. No contábamos con las bombas justo cuando la planta se estaba acomodando y en momentos en que se requería su inmediata instalación”.
“Literalmente, corrimos para insistir a la fábrica que nos adelantaran las entregas, junto con acompañar al cliente todos los días de la semana incluyendo feriados”, describe el ejecutivo.
Muy pronto la gestión del proveedor tuvo el efecto deseado: los modelos por fin arribaron a la faena. Pero luego surgió un nuevo reto. Había que llevar a cabo en forma rauda y eficiente la regulación del GAP de las bombas. El GAP es la distancia entre el tope del impulsor y la garganta de entrada a la voluta o difusor y gracias a ella se controlan las presiones en la parte posterior del impulsor.
“Finalmente, cumplimos en un 100% con la regulación del GAP poniendo en marcha los nuevos equipos de impulsión. Esta fue una gran experiencia porque no solo logramos ejecutar toda la implementación técnica en los tiempos pactados, sino que además creamos un importante vínculo con el cliente basado en la confianza”, enfatiza Toro. “Así, este trabajo dio frutos materializando la base instalada de bombas más grande del país”.
Hoy esta planta concentradora puede llegar a procesar hasta 4.600 tons/hr, gracias a su eficiente y dinámico sistema de bombeo.
Costos a la baja
Harto de las constantes fallas en la operación de sus bombas, un reconocido productor de cobre de la Región de Valparaíso decidió hacer un cambio. Su producción no despegaba y el responsable era el gran desgaste en sus equipos de impulsión, que mostraban demasiada abrasión y erosión.
“Tras un estudio en terreno junto a nuestros técnicos y luego de una exhaustiva revisión para determinar el mejor equipo para la faena, optamos por la serie S150”, explica Andrés Colomer, gerente general de Jacol. ”Esta tecnología de nuestra representada CURVE sobresale por su bajo consumo de agua y energía”.
Concluida la implementación e iniciada la puesta en marcha, la compañía minera vió cómo sus costos de operación cayeron en un 32%, enfatiza el ejecutivo. “Además, se prolongó la vida útil de cada bomba de 2 a 6 meses, a lo que se sumó una muy baja mantención de los equipos, reduciendo el TCO (Costo Total de Propiedad)”, detalla Colomer.
Mayor vida útil
En otro punto geográfico de Chile otra destacada firma minera tampoco podía seguir sosteniendo el bajo rendimiento de una de sus bombas modelo UMD 700. “Al estudiar el caso, propusimos el desarrollo de un nuevo material de revestimiento, consistente en una goma de alta resistencia a la abrasión y al desgaste”, indica Óscar Gahona, regional PLM Pumps FLSmidth.
Si bien esta tecnología ya había sido probada en equipos de impulsión de menor tamaño, detalla el ejecutivo, “era la primera vez que se ponía en marcha en un modelo de gran tamaño, convirtiéndose en una solución única en su tipo”.
Gracias a este revestimiento a la medida, la faena logró triplicar la vida útil de su bomba pasando de 1.300 horas a 4.300 horas. “De igual forma, se redujeron las detenciones de planta del cliente y se minimizaron los riesgos en materia de seguridad, al contar con menos horas de exposición a labores de mantenimiento por parte de nuestros colaboradores”, enfatiza Gahona. Gracias a toda esta gestión, las paradas de planta disminuyeron de 7 al año a solo 2.
Asimismo, se triplicó la duración de los componentes internos de la bomba, al tratarse de un revestimiento mucho más resistente “y la empresa minera logró ahorrar un 7% en consumo de energía”, asevera el ejecutivo.
Ahorro en agua
Mientras esta faena alzaba ambos brazos en señal de satisfacción, el mayor yacimiento subterráneo de cobre del país desanimado observaba su bomba de pulpa.
“Este presentaba una baja duración de sus componentes wet-end y fallas constantes en las camisas protectoras del eje. De hecho, se registraban fallas a las 500 y 800 horas de operación”, explica Mitchell Vivanco, jefe Ventas Minería – Zona Centro de KSB Chile.
El diagnóstico era inminente: había que adoptar otro equipo con mejores prestaciones técnicas. Así, los operadores de la empresa minera decidieron probar el modelo KSB – GIW® MDX.
“En tiempo récord instalamos la nueva tecnología solucionando el problema de origen”, detalla el ejecutivo. “El nuevo modelo brinda 6.000 horas de campaña completa con una sola parada para cambio de impulsor y laina a las 3.000 horas de operación versus las paradas cada 1.500 horas del anterior modelo”.
Pero lo mejor no fue el desempeño del nuevo equipo. La compañía minera logró un ahorro de nada menos del 60% en consumo de agua de sello, “gracias al sistema spiral trac de nuestro modelo”, subraya Vivanco.
Mejorado perfomance
Paralelamente, en la escena nortina del país, otra importante empresa minera creyó que todo marcharía a la perfección tras adquirir bombas bajo molino Warman de gran tamaño, para un importante proyecto en la zona. Así fue durante un tiempo hasta que aparecieron ciertos inconvenientes.
“Si bien el cliente optimizó sus circuitos de chancado y molienda, aumentando el tonelaje fresco y su capacidad de tratamiento del mineral, los componentes de las bombas instaladas redujeron su duración producto de la mayor exigencia operacional”, explica José Antonio Bautista, ingeniero de aplicaciones experto Weir Minerals. “En consecuencia, la faena aumentó las detenciones para poder realizar mantención a sus equipos de impulsión”.
La faena no se cruzó de brazos y solicitó una solución para mejorar la duración de los componentes y retomar las estrategias de mantención previas al aumento de capacidad.
“Llevamos a cabo el diseño e implementación de una propuesta de upgrade, que consistió en reemplazar los wet end instalados por unos con nuevo diseño hidráulico”, describe Bautista. “El objetivo era mejorar la duración de los componentes y la predictibilidad del patrón de desgaste, aumentando la confiabilidad operacional”,
Los resultados arrojaron un cualitativo salto para la minera, ya que antes había que realizar un reemplazo del disco de succión a las 1.300 horas y con el upgrade realizado la duración del dispositivo aumentó a 2.800 horas, recalca el ejecutivo.
Bombeo de agua
En otras latitudes geográficas del globo, un reconocido productor estadounidense de minerales apostaba por aumentar la eficiencia de su operación y para ello requería de un buen sistema de impulsión capaz de manejar el agua de fondo de mina.
“Luego de estudiar bien el proyecto del cliente, la mejor opción era la bomba de cebado asistido serie PAH Prime Aire Plus del fabricante estadounidense Gorman- Rupp, nuestra representada”, explica Francisco Salinas, PM Gorman-Rupp de Soltex Chile. “Este modelo se adapta a la geometría del terreno, trabajando desde fuera del cuerpo del agua, sin necesidad de costosas y complejas obras civiles, consolidándose como una exitosa alternativa frente a los sistemas de bombeo flotantes y de turbina vertical sumergibles que suelen utilizarse en estos casos”.
“De hecho, este equipo PAH10A60C-B (12” x 10”) es capaz de bombear hasta 14,000 m³/h de agua con sólidos y a una altura total de 155 metros a válvula cerrada”, describe el ejecutivo. “En síntesis, ante grandes volúmenes de agua con sedimentos que necesitan elevarse a gran altura, este equipo reduce al mínimo las fases de rebombeo, lo que se traduce en importantes ahorros”.
Tras una rápida y fácil instalación, la compañía minera ganó mayor confiabilidad en la operación, enfatiza Salinas, “con un bajo mantenimiento, permitiendo a los operadores reducir el tiempo de inactividad, reduciendo su TCO, el consumo de energía y sus costos de mano de obra”.