Infraestructura portuaria: Logística competitiva
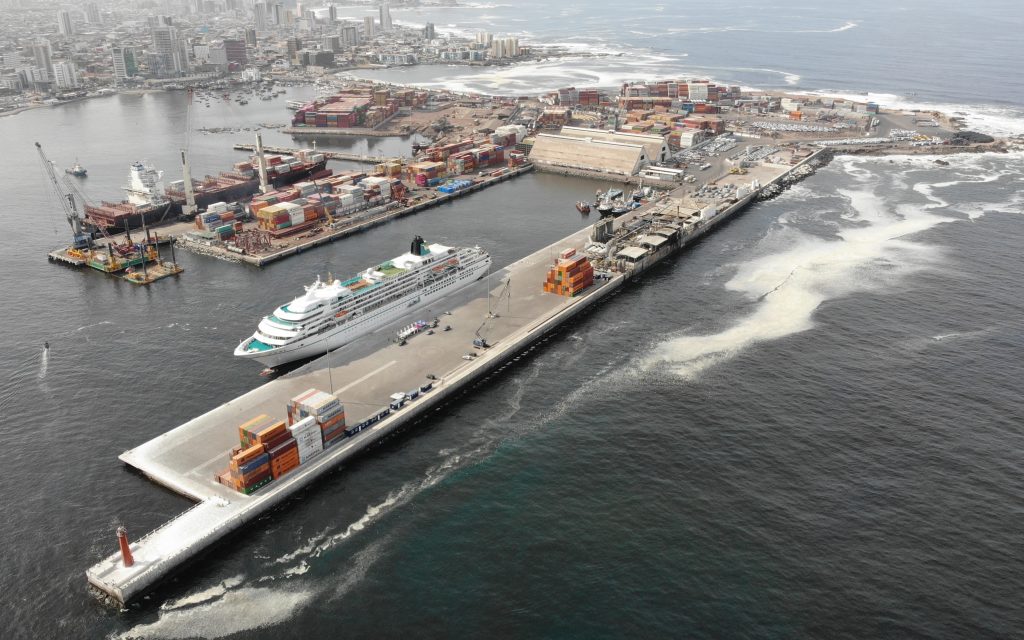
Con más tecnologías automatizadas y energías limpias para reducir su huella de carbono, la logística portuaria cumple la promesa de brindar excelencia y seguridad operacional a uno de sus principales socios: la minería.
Por Marina Parisi
_____________________
A lo largo de sus 28 años de vida Puerto Punta Padrones de Minera Candelaria (Lundin Mining) y emplazado en la Región de Atacama, ha atendido 931 naves y ha embarcado más de 16 millones de toneladas de concentrado de cobre.
Lo anterior gracias a que sus dos infraestructuras principales (edificios de descarga y de almacenamiento) operan con diferencial de presión negativa. Vale decir, los colectores de polvo evitan la salida de partículas de concentrado hacia el entorno, mientras que las correas transportadoras están encapsuladas, impidiendo así el contacto del material con el exterior.
Mientras, las labores de embarque están a cargo del Shiploader (cargador móvil) desplazándose a lo largo del barco y evitando que la nave tenga que maniobrar. Así, el carguío es más eficiente. El Shiploader además está provisto de un chute telescópico de cuatro cuerpos que se interna en la bodega del barco.
En el extremo del chute telescópico hay un repartidor de carga instalado que gira en 360°, distribuyendo el material de forma uniforme en la bodega. Dicha tarea es realizada por un operador desde la cubierta mediante una consola de control remoto.
Todo esto y más es supervisado por Marcia Soto, subgerenta de operaciones Puerto y Planta Desalinizadora, la primera mujer en ocupar este cargo en la historia de la compañía.
“Llevamos más de 10 años sin incidentes con daños a personas y éste sigue siendo nuestro principal foco, además de mantener los elevados estándares de operación”, indica la ejecutiva.
“La prioridad es estar siempre preparados para responder a todos los requerimientos que demande Candelaria para su proceso productivo, combinando y equilibrando este proceso con la cultura de minería responsable, uno de nuestros valores siempre presente”, subraya Soto.
Reconstrucción post terremoto
La tarde del 1° de abril del 2014 finalizaba en total normalidad para la Empresa Portuaria Iquique (EPI). Inesperadamente, a las 20.46 hrs comenzó a temblar hasta alcanzar los 8,2 Richter. Lo peor sobrevino al día siguiente: una réplica de 7,6 volvió a azotar al complejo.
“Ambos terremotos dejaron al puerto inoperativo y en riesgo de colapso, comprometiendo su continuidad operacional”, asevera Rubén Castro, gerente general de EPI, ubicado en la Región de Tarapacá.
El 80% del frente de atraque resultó dañado con desplazamiento de muros, además de pérdida en la verticalidad y grietas en las paredes de los bloques que componen el muro. Es que el diseño original del complejo no había experimentado cambios desde 1930.
“La solución implicaba reconstruir todo el puerto y su rompeolas a un costo de US$400 millones con tres años de paralización en la atención a naves”, precisa Castro. “Ante este escenario desarrollamos otro diseño de ingeniería más eficiente, moderno y competitivo”.
Este incluyó una solución antisísmica consistente en micropilotes distribuidos a lo largo de todo el frente de atraque, explica el ejecutivo. “Los micropilotes atraviesan los bloques de hormigón y el prisma anclándose al estrato de las rocas. Ello sumado al coronamiento de la losa de hormigón, estabiliza los muros de los bloques transformándolos en estructuras monolíticas y estables”.
Con el nuevo diseño la empresa ganó 100% de seguridad en sus sitios N°1 y 2 y optimizó el ancho de su losa en 5.5 metros por un largo de 403 metros. “Así, logramos mayor profundidad pasando de 9 metros a 11,4 metros de calado autorizado, mejorando nuestra oferta de servicios con una inversión de US$52 millones”, concluye Castro.
Combustibles verdes
Uno de los objetivos que persigue Puerto Ventanas (PVSA), emplazado en la Región de Valparaíso, es incrementar la sustentabilidad de sus operaciones mitigando su huella de carbono. Para ello implementó un complejo de energía undimotriz en 2021, a partir de energía generada por las olas de mar.
“El proyecto, desarrollado en alianza con la empresa Alü Energy, consideró la instalación en el extremo poniente del sitio N°5 de un SCU (Sistema Convertidor Undimotriz)”, describe Luis Fuentes, gerente de Sostenibilidad y Personas de PVSA. “Este sistema permite captar energía desde un medio renovable no convencional como el oleaje marino, para transformarlo en energía estable, limpia y más competitiva”.
El SCU fue desarrollado 100% en Chile y es único en su diseño, enfatiza el ejecutivo. “Considera un octógono flotante que conlleva un mecanismo convertidor del movimiento provocado por el oleaje, conectado a un generador desde donde se transmite la corriente a tierra”.
En una primera etapa la iniciativa apunta a abastecer de energía a los servicios del puerto, indica Fuentes, con la opción de escalar el proyecto a mayores niveles de producción. “Actualmente, estamos levantando indicadores para corroborar cuánta energía podemos producir en esta primera etapa”.
Tecnología electrónica ad hoc
Otro actor enfocado en introducir importantes mejoras es Puerto Mejillones, quien hoy se encuentra en una actualización del movimiento de carros ferroviarios en la zona de acceso de trenes en su área de concentrado.
Esta iniciativa apunta a transformar el sistema de arrastre en uno controlado, mediante VDF (Variadores de Frecuencia), para mejorar la confiabilidad del servicio que brinda el complejo ubicado en la Región de Antofagasta.
Al incorporar los variadores al sistema eléctrico de huinches se puede controlar sus flujos y velocidades de operación, “eliminando las perturbaciones de las líneas eléctricas y el estrés mecánico donde se movilizan los convoyes de los trenes”, precisa Wilfredo Rojas, jefe comercial de Puerto Mejillones.
El proyecto ya se encuentra en etapa final de comisionamiento y pruebas de carga, afirma Drago Torres, jefe de proyecto de Puerto Mejillones. “Esta iniciativa refuerza la continuidad en el proceso de transferencia de carga de graneles optimizando la seguridad y excelencia de la operación”.
La nueva arquitectura con VDF además redundará en un ahorro significativo en consumo energético, “ya que solo se consumirá focalizadamente y de acuerdo a las necesidades del proceso”, grafica Rojas. “La tecnología electrónica es cada vez más utilizada en nuestra industria, contribuyendo a desarrollos avanzados en la automatización y estandarización de los procesos”.