Hacia la robotización y nueva forma de hacer los recambios
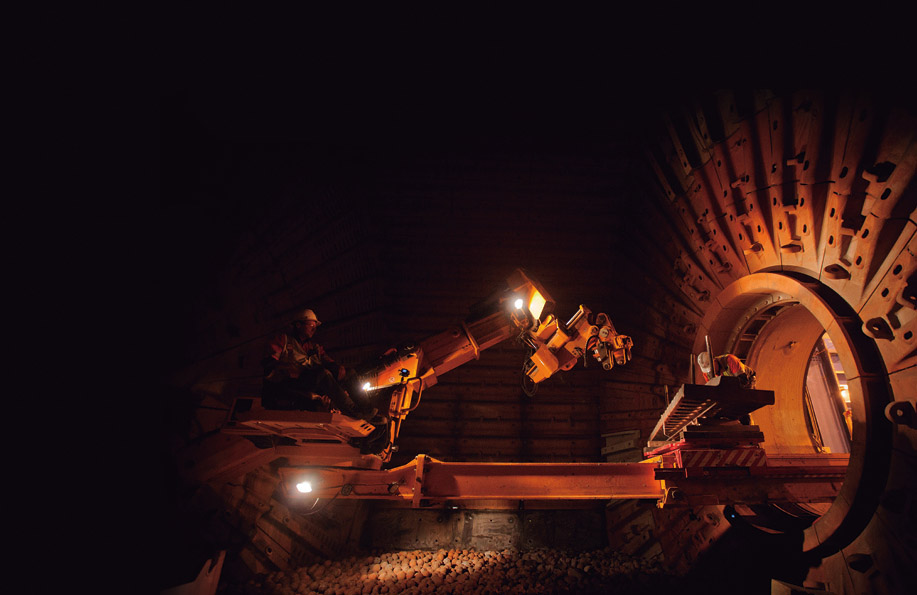
Con innovaciones, se calcula posible un rendimiento adicional del 2% en la operación del molino, lo que aumentaría un 5% la rentabilidad.
Por Eric Rivera, Desde Viña del Mar
En las plantas concentradoras de mineral, las detenciones por mantenimiento programado constituyen la mayor pérdida de tiempo de operación, por lo cual es clave minimizar el tiempo para cada aspecto de la detención, siendo muy relevante el cambio de revestimientos del o los molinos.
El tema está cada vez más presente en la industria, ya que se advierte una cierta “madurez” en el enfoque del problema de los revestimientos, coinciden especialistas. Hace algunos años, el enfoque apuntaba exclusivamente a un tema de mantenimiento, cuidar el molino del desgaste, poner la protección y dar un perfil para que no resbale la carga, pero sin mucho análisis del impacto de eso en la producción y el proceso.
Años después se empezó a tomar conciencia que junto con la protección del revestimiento, debe entenderse que es el componente que entrega la energía desde el molino a la carga, y cómo lo haga influye fuertemente en el desempeño del equipo. Pero aún faltaba un análisis más completo, lo que ya se estaría dando actualmente.
“Ahora último vemos que el análisis no sólo se ocupa de la mantención y la energía, sino que al ser el molino parte de una planta, sus mejoras deben ir a la par con los cuellos de botella, y ver qué efecto tienen en el molino siguiente. A esto se suma un análisis más detallado de costos, relacionando dimensiones con procesos, con mantenimiento y posibilidades de recambio. Así que ahora hay un análisis más sistémico, una visión más profunda del tema”, explica Waldo Valderrama, académico del Departamento de Ciencias de Materiales de la Universidad Técnica Federico Santa María e integrante del comité organizador del congreso de revestimientos Revemol, que se realizó recientemente en Viña del Mar.
A juicio del académico, las tendencias señalan que es posible asegurar la confiabilidad y la seguridad mediante la automatización del recambio. Una tarea que debe hacerse en condiciones de riesgo, en ambiente confinado, moviendo grandes pesos y trabajando sobre una superficie inestable.
Para ello, la empresa Russell Mineral Equipment (RME) hizo un estudio identificando dos tecnologías para el mejoramiento del recambio de revestimientos. La primera fue la automatización del retiro y apernado de las placas, lo que implica rediseñar revestimientos y tuercas para su manejo robotizado, que aumenta la rapidez y seguridad de la operación.
La automatización propuesta por RME abarca todas las actividades externas, control de los martillos Thunderbolt, reemplazo de la tuerca/golilla, reemplazo y retiro del tapón y limpieza de los agujeros, cambio automatizado de herramienta, retiro e instalación automatizada de revestimientos y pernos, transporte automatizado de revestimientos, y acceso a puntos altos dentro y fuera del molino.
La otra innovación identificada por Russell para optimizar el recambio es la aplicación del denominado “flujo unitario de la Filosofía Lean”.
Peter Rubie, gerente general de Russell, explica que la automatización permitirá cambiar la secuencia del trabajo de recambio, que actualmente se realiza mediante el sistema de flujo por lotes.
“En vez de soltar primero los revestimientos y en otro giro del molino colocar los nuevos, con el equipo robotizado será posible soltar y cambiar cada revestimiento a la vez, lo que reducirá los tiempos del trabajo y el personal requerido”, precisa el ejecutivo, aunque aclara que los técnicos que operen la maquinaria deberán tener “alta calificación”.
Como meta, RME espera lograr una reducción promedio de 12 horas en el tiempo de recambio actual, el que en todo caso difiere según cada mina y cada planta, aunque se trate de molinos similares. Ya desde la aplicación del sistema de recambio creado por RME, los tiempos promedio de recambio han bajado desde un rango de 150-200 horas a 60-150, y se espera que a futuro desciendan a rangos entre 40 y 70 horas, según dio a conocer John Russell, CEO y fundador de la empresa, en el marco del congreso Revemol.
Mediante estos avances, que abarcan tecnología dura y cambios al diseño del trabajo, se reducirían los riesgos de accidentes, que siguen presentes pues es muy difícil calzar las fechas de mantenciones con la disponibilidad de los equipos humanos. Las cuadrillas de mantenimiento siempre tienen algún personal sin la experiencia suficiente, y la mayor parte de los accidentes afectan a esos trabajadores.
“Siempre se producen imprevistos, pues la planificación de la faena de mantenimiento, no considera la globalidad y no involucra a proveedores o contratistas secundarios o revisiones del estado de máquinas. Y en esos aspectos secundarios o laterales hay factores de pérdidas e ineficiencia. Por eso la tendencia apunta a una operación más mecanizada y tecnificada pero más segura”, destaca Waldo Valderrama.
Otra clave para planificar y lograr una mantención más corta consiste en predecir los tiempos de cambio de revestimientos del molino de manera más precisa, usando la simulación de elementos discretos como el software “Mill Reline Director” de RME.
Esta herramienta identifica como aspectos de fuerte impacto el diseño de los revestimientos, las habilidades y la gestión del personal, y la selección y confiabilidad del equipamiento.
El simulador se perfila especialmente útil a los diseñadores de planta para que los proyectos greenfield optimicen el cambio de revestimientos y eviten las restricciones.
Como resultado de incorporar estas innovaciones, Russell Mineral Equipment calcula que es posible obtener un rendimiento adicional del 2% en la operación del molino, lo que representaría un incremento de 5% en la rentabilidad, al estar ya pagados los gastos generales.
Fuente: NME