Las nuevas experiencias en automatización minera
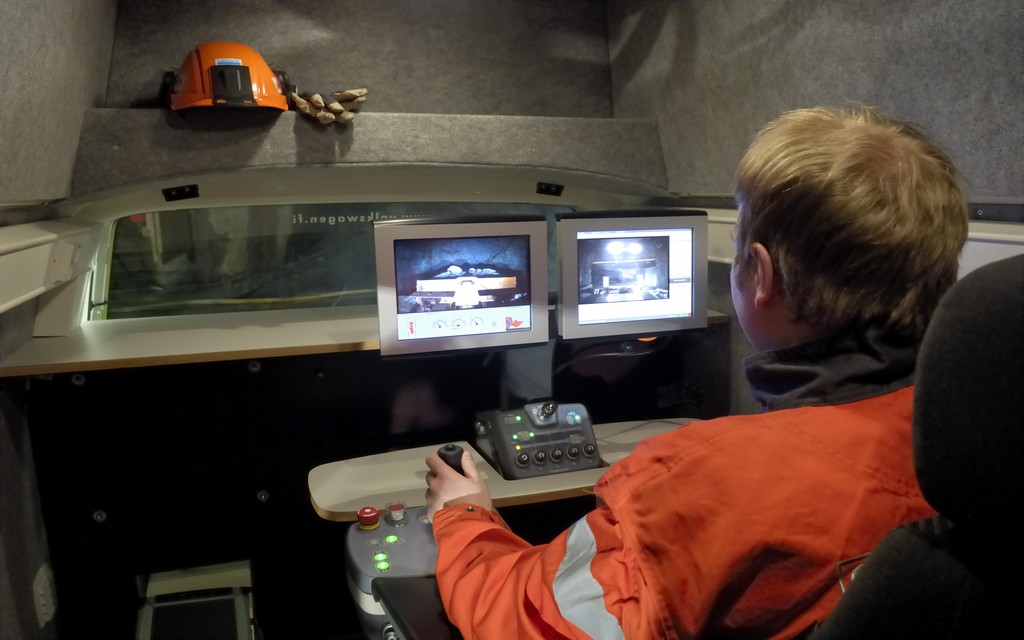
(Foto: Sandvik)
A un ritmo cada vez más vertiginoso, las compañías mineras a nivel mundial están buscando digitalizar y automatizar sus operaciones para lograr ser más eficientes.
Por Daniela Tapia
Revista Nueva Minería y Energía
______________
Es una realidad que llegó para quedarse. Cada vez más las compañías mineras a nivel mundial están buscando digitalizar y automatizar sus operaciones para lograr ser más eficientes, aumentando así la productividad y disminuyendo los costos y los riesgos.
En Chile, yacimientos como Chuquicamata y El Teniente, por ejemplo, han incorporado distintos tipos de tecnologías para automatizar procesos, especialmente aquellos más riesgosos. Pues al manejar las máquinas a control remoto, es posible mejorar la seguridad, ya que no es necesario que haya personas en zonas peligrosas y en momentos críticos.
Es así como camiones controlados a distancia, brazos robóticos que realizan labores consideradas peligrosas para los trabajadores -quienes pueden manejarlos a distancia a través de distintos dispositivos, como pantallas táctiles, ubicadas en una sala de control dispuesta en cualquier parte del país-, ya forman parte de la estrategia de operación en la industria.
Un estudio de Ericsson, de hecho, confirmó la importancia de este fenómeno. Según el análisis, la automatización de los procesos, en el caso de la perforación, podría lograr un aumento de un 40% en horas de operación. Un potencial que puede ser aprovechado en un país minero como Chile y que sería clave para mantener la competitividad en el mercado internacional.
Así las cosas, en un contexto donde la minería ha representado en torno al 10% del PIB en la última década y es la industria que encabeza las exportaciones nacionales, las posibilidades que ofrece la digitalización y la automatización para la minería chilena resultan significativas a la hora de pensar el futuro del sector.
Con el fin de conocer los avances que se han implementado en el área de la automatización para la minería, Revista Nueva Minería y Energía recogió algunos de los casos más interesantes que han desarrollado algunos centros de investigación en esta materia. Los invitamos a conocer estas experiencias en las siguientes páginas.
La solución innovadora del AMTC
El Centro Avanzado de Tecnología para la Minería (AMTC por su sigla en inglés) destaca una solución que promete mejorar la productividad de una operación minera.
En abril pasado, el centro publicó los resultados de un proyecto Fondef de desarrollo de un sistema de carguío autónomo para cargadores frontales de bajo perfil (LHD). Consiste en dotar a un LHD de la capacidad de hacer funcionar, sin un operador humano, la pala con la que se extrae el material rocoso del caserón en una mina subterránea.
¿Cómo funciona? El vehículo se acerca al punto de extracción autónomamente, evalúa mediante sensores el tamaño y granulometría del material a extraer y sobre la base de esa información decide la fuerza a aplicar en la pala, la manera de moverla y otras variables. Este sistema es además, de carácter colaborativo: si por algún motivo el LHD no puede realizar su tarea, avisa a un operador humano, situado en una sala de telecomando que puede estar a kilómetros de distancia, para que efectúe la carga.
“Para este proyecto vanguardista trabajamos en colaboración con la empresa proveedora GHH, que nos facilitó equipos y terrenos para pruebas y validación”, dice Javier Ruiz del Solar, director ejecutivo del AMTC.
Desde la entidad también señalan que, además de automatizar la última tarea que quedaba por robotizar en un cargador frontal, pues la navegación autónoma ya existe (como en el caso de la mina Chuquicamata Subterránea de Codelco), esta solución tiene el valor adicional de apuntar específicamente a la mediana minería, que hasta hoy no tenía acceso a esta tecnología por ser, en principio, de muy alto costo.
“Nuestro proyecto permite automatizar un vehículo ya existente y las empresas mineras no tienen que adquirir un equipo automatizado de origen, con sensores incorporados. Asimismo, aumentamos la seguridad laboral al alejar al operador humano del ambiente riesgoso de la faena subterránea, donde está expuesto a accidentes potencialmente fatales”, añade el ejecutivo del centro especializado.
El valioso apoyo de Expande
El programa Expande, una iniciativa público-privada codiseñada e implementada por Fundación Chile y sus socios estratégicos, ha sido un aliado a la hora de mejorar el desempeño de la industria minera a través del apoyo que les ha brindado a distintas compañías proveedoras, que se han especializado en el rubro de la automatización, entre otras áreas.
Una de estas firmas es ETT, la cual tras 20 años visitando molinos SAG alrededor del mundo, creó SAG Scanner, un sistema de instrumentación de naturaleza óptica que, posicionado estratégicamente dentro del molino SAG, permite recoger datos y monitorear el interior del mismo sin necesidad de detenerlo totalmente.
Hoy los usuarios de SAG Scanner (operaciones, mantenimiento y metalurgia) han confiado en esta herramienta porque permite aumentar la disponibilidad del molino, maximiza el uso de revestimiento y optimiza el proceso de conminución a través de la determinación del collar de bolas y la distribución de la carga al interior del equipo.
Actualmente, SAG Scanner está completando pruebas pilotos en las plantas concentradoras más importantes de la gran minería, con lo cual se espera que las ventajas de su implementación signifiquen beneficios por sobre los US$4 millones.
Por otro lado, destaca Aiko, empresa de vasta trayectoria en la generación de soluciones tecnológicas, que ha desarrollado Fuel Explorer, solución que permite medir en tiempo real el nivel de llenado de combustible. ¿El fin? Permitir de esta manera, hacer uso efectivo de la capacidad del estanque, lo que se traduce en menores ciclos de recarga de combustible y mayor utilización operacional del equipo.
La tecnología consta de un sensor instalado en la parte inferior del estanque, cuya información se transmite a una plataforma tecnológica interoperable con otras, como por ejemplo, el sistema dispatch de la mina, permitiendo disponibilizar la información para la correcta toma de decisiones.
“El impacto es tal que, para una flota de 100 camiones, se puede tener un beneficio aproximado de US$30 millones al año en aumento de productividad”, dice Enrique Molina, director Ejecutivo de Expande.
La tecnología se ha puesto en marcha en importantes operaciones a rajo abierto en Chile, tanto en flotas de equipos convencionales como en camiones autónomos.
Un interesante aporte desde la academia
Un grupo de investigadores liderado por el profesor Aldo Cipriano, del Departamento de Ingeniería Eléctrica de la Pontificia Universidad Católica, en colaboración con el profesor Miguel Herrera, de la carrera de Ingeniería en Minería de la Universidad Adolfo Ibáñez (UAI), desarrollaron un analizador de calidad de mineral para los procesos de aglomeración y curado para plantas de extracción de cobre, de tipo hidrometalúrgicas.
Herrera comenta que se idearon dos prototipos que asisten al operador en la toma de decisiones. Por ejemplo, el manejo de las tasas de dosificación de agua y ácido, a fin de optimizar la calidad del mineral curado y aglomerado. Los prototipos desarrollados son: SIMRIS, un sistema de monitorización remota y en tiempo real de imágenes y señales; y ACMA, un analizador de calidad de mineral aglomerado.
“Con esta tecnología, es posible medir en línea a la salida del tambor de curado y aglomeración las variables relevantes del proceso como son la temperatura, humedad, distribución de tamaño, forma y perfil del mineral en una correa transportadora, que mueve el mineral a una pila de lixiviación”, agrega el académico.
De este modo, es posible optimizar el curado y aglomeración, produciendo glómeros de alta calidad que optimizan la cinética global y la eficiencia metalúrgica del proceso de lixiviación.
A la fecha, -señala Herrera-, esta tecnología ha sido testeada en la Planta Mantoverde de Mantos Copper y en la Planta Manuel Antonio Matta de Enami, permitiendo un monitoreo en tiempo real y de apoyo al operador en la toma oportuna de decisiones y ejecución de acciones que aseguren un rendimiento óptimo.
“El sistema presenta los datos medidos y las variables estimadas con errores de 0.5 – 2%, garantizando la calidad de aglomeración y curado. Sin lugar a dudas, la implementación de esta tecnología en procesos hidrometalúrgicos tiene capacidades de crecimiento significativas y es un paso relevante para la automatización del curado y aglomeración de minerales”, afirma el profesor de la UAI.