Correas transportadoras: Monitoreo en tiempo real
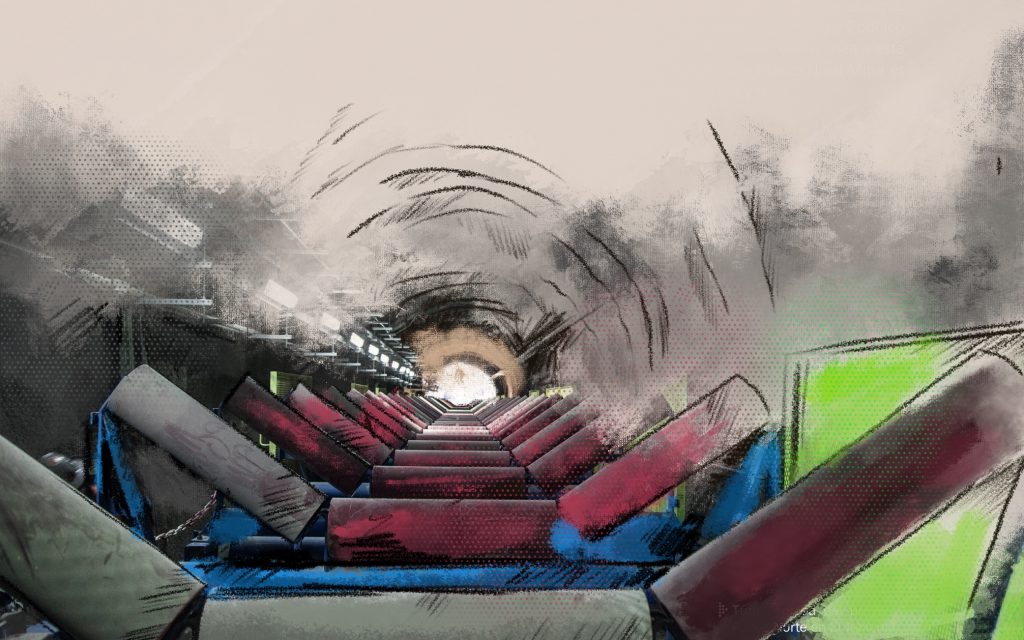
Ya no se trata de prevenir paradas catastróficas. Hoy se requiere de sofisticados sistemas para monitorear en tiempo real toda la operación de la correa, si la meta es aumentar la productividad minera y reducir costos.
Por Marina Parisi
________________
Cuando años atrás Codelco decidió transformar su mina subterránea El Teniente en el proyecto Nuevo Nivel Mina, incorporó una novedosa forma de transportar el mineral. En vez de hacerlo a través de camiones, lo haría mediante un túnel correa de nueve kilómetros de longitud.
Tras varios estudios de factibilidad que indicaban que ésta era una excelente opción, arrancó la construcción del túnel correa en la zona de Andes Norte y a más de 700 metros de profundidad. Pero en 2018 aparecieron los primeros obstáculos. “La sismicidad que hemos enfrentado ha sido una gran reto y este fenómeno va a continuar”, explica Jorge Suazo de Codelco. “Al tronar o excavar se extrae una parte del macizo rocoso, el cual después necesita redistribuirse produciendo una energía vibratoria que impacta en el resto del macizo y dañando el túnel”.
“El problema es que a veces el daño se proyecta en zonas del túnel que ya hemos fortificado y esta situación se intensifica a medida que nos acercamos cada vez más al corazón de la mina. Por ello, hemos tenido muy pocos avances el último tiempo”, detalla el ejecutivo. “Aún quedan 400 metros para concluir el túnel correa, que son justamente los más complejos y esperamos que la puesta marcha sea este año o el 2025”.
De momento, la estatal continúa desarrollando este proyecto, en forma pausada y cuidadosa garantizando la seguridad de sus trabajadores y apoyándose en tecnologías de última generación, como el marco dinámico que permite una mayor absorción de energía. Sin embargo, a juicio de los expertos, a futuro Codelco deberá incorporar sistemas de monitoreo en línea a esta cinta transportadora, si la meta de Nuevo Nivel Mina es producir 180 mil toneladas al día y más.
“Uno de los principales activos en minería son las correas transportadoras y al incorporar sistemas de monitoreo a estas cintas, se reduce o elimina la inspección física del operador, mejorando la gestión del equipo, incrementando la productividad de los activos y elevando los estándares de seguridad”, asevera Andrés González, gerente general del Centro Nacional de Pilotaje (CNP).
Nuevas tecnologías
De hecho, ya han aparecido una serie de tecnologías a partir del uso del IIOT (Internet de las Cosas Industrial), para el análisis y seguimiento de las condiciones de la correa, precisa el experto, “que pueden prevenir problemas de mantenimiento, fallas como incendios, o bien, dificultades que se traducen en paradas imprevistas y riesgos operacionales adicionales”.
En este sentido y desde su rol de acelerador en el desarrollo de nuevas tecnologías, el Centro Nacional de Pilotaje ya ha validado soluciones nacionales e internacionales, a partir del monitoreo en tiempo real de toda la operación de transporte y manejo de materiales.
“Realizamos un piloto para la empresa chilena Rivet para su tecnología Rollvolution, que posibilita el seguimiento inalámbrico de la temperatura y la vibración en rodillos”, explica González. “Durante el testeo se contrastaron los datos que entrega la tecnología con sensores tradicionales y se generaron fallas inducidas, detalla, “permitiendo así comprobar el buen desempeño y el potencial de poder emplear los datos recogidos”.
“Otras tecnologías que hemos observado son las que emplean sensores de sacrificio y que se arrojan sobre las correas, con cuyos datos se logra un monitoreo instantáneo de toda la cinta”, describe el experto. “Mientras que otros desarrollos más recientes utilizan la fibra óptica como sensor, posibilitando un seguimiento en tiempo real y con gran precisión”.
Ingeniería de la confiabilidad
Para Felipe Maldonado, Engineering Manager – VIRTA de Fluor, el monitoreo de los componentes de la correa transportadora “ha significado un hito en la operación de estas herramientas, permitiendo el control de motores, poleas, polines y estado y desgaste de la cinta. De esta forma, el cliente final puede contar con un diagnóstico eficiente de su equipo”.
Pero el seguimiento de las condiciones de operación no solo posibilita un diagnóstico del equipo y la detección preventiva de fallas catastróficas, añade Gerardo R. Díaz, Material Handling Expert de Fluor. En su opinión, es también un eslabón clave para el diseño de un sistema de mantenimiento centrado en la ingeniería de la confiabilidad.
“Los datos gestionados por un sistema de planificación de recursos empresariales (ERP) o equivalente, y que alimentan directamente a un sistema de mantenimiento centrado en la ingeniería de la confiabilidad, permiten la planificación, programación, asignación y ejecución del mantenimiento en forma dinámica, orientando los esfuerzos en la criticidad de los procesos/equipos y minimizando los costos de mantenimiento y de capital”, sostiene el experto.
“Otro aspecto muy importante en torno al mantenimiento centrado en la ingeniería de confiabilidad”, plantea Díaz “es que posteriormente con los datos específicos de la operación en mano, se puede diseñar un ciclo de mejoramiento continuo a lo largo de toda la vida útil de los activos”.
Lo anterior bien puede culminar en la eficiente resolución de un problema, como el que Díaz relata a continuación. “Logramos concluir tempranamente que la baja confiabilidad del sistema de chancado y correas en una empresa minera, tenía su origen en el incorrecto montaje mecánico del sistema motriz, durante su construcción (mortalidad infantil). Dicha conclusión fue posible gracias a los sistemas de monitoreo continuo de condiciones; la gestión de su data vinculada a un sistema de mantención centrado en la confiabilidad; las métricas obtenidas; y el análisis de causa-raíz”.
Y si bien el origen del contratiempo puede ser otro, en opinión de Maldonado, la supervisión de la operación en tiempo real es vital para resolver cualquier evento.
“A modo de ejemplo: las reiteradas dificultades en la correa transportadora de un cliente obligaron a solicitar un estudio, ya que una polea deflectora presentaba constantes fallas durante la operación”, describe el experto. “El sistema de monitoreo indicaba incrementos de vibración a medida que el tiempo de uso transcurría, desencadenando fallas si la polea no era cambiada a tiempo”.
El tema es que el recambio de polea puede tardar varios días, dependiendo de los accesos y herramientas que se tengan disponibles, asegura Maldonado, “perjudicando la producción de la planta e incrementando los costos. Al final el estudio concluyó que la polea había sido mal diseñada, y al momento de la partida, ésta anotaba un peak de tensión que excedía los valores de diseño originales del proyecto. Se cambió la polea y se aumentó en 15 segundos la rampa de partida respectivamente (de 15s originales se terminó en 30s)”.
Oportunidad para proveedores
Si bien el eficiente monitoreo de la operación hoy concita la atención de la industria, las correas transportadoras también han experimentado notables avances en sus características técnicas. Uno de ellos es el aumento en su capacidad de transporte del material, especifica Mauricio Tapia Rubilar, consultor principal de M&G Consultoría Minera, “lo que se ha logrado gracias al desarrollo de cintas más resistentes y la optimización de los mismos sistemas de transporte”.
En paralelo, los fabricantes han innovado desarrollando nuevos materiales, tanto para las correas y sus componentes como también para sus sistemas internos, apunta González. “Incluso, algunos de estos nuevos materiales pueden predecir cortes. Asimismo, hemos visto nuevos materiales que sirven para realizar reparaciones. En síntesis, hay un espacio importante para mejorar e innovar con soluciones que optimicen la mantenibilidad, similar al concepto de Pit Stops de Fórmula 1, tanto en correas como en chutes”.
Aunque los proveedores ya han acertado en una primera instancia, subraya Tapia, “desarrollando dispositivos de parada de emergencia y de detección de desalineación. Estas herramientas han incrementado la continuidad operacional, disminuyendo en forma considerable el porcentaje de interrupciones y paradas”.
Desafíos por delante
Pese al esfuerzo desplegado por los proveedores de esta industria, aún quedan varias vallas en el camino, mientras las empresas mineras demandan soluciones cada vez más eficientes para aumentar la productividad y mantener los costos a raya.
En este sentido, para González un reto importante es la implementación de los IPCC (In Pit Crusher and Conveying), “que permiten reducir el CAPEX y los tiempos de ciclos, complementando el actual sistema de pala y camión. Si bien se trata de configuraciones diferentes, hay que analizarlas en la medida que permitan dar nuevos escenarios al negocio. Como todo cambio al que nos enfrentamos, no están exentos de cuestionamientos y resistencia por parte de los tomadores de decisión. Por ello, es en este escenario que las pruebas pilotos son necesarias para reducir el riesgo”.
En tanto, Maldonado plantea que un desafío pendiente por parte de los fabricantes, es entregar el producto en plazos acotados, “los que son cada vez más desafiantes. Asimismo, hay que brindar soluciones del tipo ´estado del arte´, con capacidad de cubrir necesidades de manejo de mineral cada vez mayores. Este es un gran reto hoy considerando las bajas leyes del cobre”.
Mientras que Díaz apunta a un desafío más bien cultural. En su opinión, una de las principales tareas de los fabricantes “es apoyar a los clientes para que comprendan que el costo y el diseño adicional, a raíz de múltiples sensores y subsistemas para la implementación de los sistemas de monitoreo continuo de condiciones, son sinónimo de ahorro a largo plazo gracias a la mejora en la operación y maximización del uso de los activos para el negocio”.
“Tampoco hay que olvidar la importancia del trabajo en equipo junto al cliente final”, acota Maldonado, “ya sea en labores de mantenimiento como también de producción, para así poder aplicar y sacar el mejor partido de las ventajas que ofrece el mercado”.
A todo este conjunto de tareas, Tapia añade una muy importante: “la regulación más estricta hoy exige soluciones más sostenibles. Por lo tanto, los fabricantes deben asumir el reto de desarrollar equipos, herramientas y sistemas que reduzcan la huella de carbono, desde el uso de materiales sostenibles hasta la implementación de tecnologías más limpias y eficientes en términos energéticos”.