Nuevas estrategias para optimizar recambio de correas mineras

Cambiando la forma de hacer las cosas, las empresas logran rebajar tiempos y costos en la reparación y operación de estos sistemas de transporte.
Eric Rivera
Desde Viña del Mar
Revista Nueva Minería y Energía
________________
Después de una evidente caída en las ventas de correas -el año pasado fueron un 60% menos que el peak de 2012-, el mercado de cintas transportadoras pareciera estar recuperándose, en línea con las mejores perspectivas de la industria, aunque todavía de manera tímida, advierten algunos actores del rubro.
“Para este año esperamos un repunte del orden del 10%. No es mucho, pero es un cambio de tendencia”, reconoció Alex Cantzler, gerente General de la empresa Simmatrans, en el marco del reciente congreso de correas transportadoras Belt 2017, que se realizó en Viña del Mar.
Pero las principales compañías del sector todavía ven el futuro con cautela, tras pasar difíciles momentos durante los últimos años. Por eso, el enfoque actual hace énfasis en la eficiencia de los procesos, y en implementar planes que se orienten a reducir costos, planificar y conseguir ahorros.
Junto con probar productos y tecnologías, las mineras buscan optimizar especialmente los procesos vinculados al mantenimiento, cambiando la manera de enfocar el trabajo para rebajar costos. La División Chuquicamata de Codelco, por ejemplo, aplicó una nueva planificación para las reparaciones, pasando del trabajo reactivo a un esquema proactivo y estratégico que trajo positivos resultados.
Este cambio de enfoque al mantenimiento produjo una fuerte reducción de los tiempos de reparación con rebaja de costos y aumento de la productividad, según destacó René Galleguillos, gerente de Mantenimiento, Servicios y Suministros de la División Chuquicamata de Codelco, en el marco del Congreso Belt 2017.
Otras medidas apuntaron a la calidad de los empalmes, punto donde se producen las roturas de las correas. Se estableció una estrategia de aseguramiento y estandarización del traslado y almacenamiento de materiales y equipos para reparar correas, como también sobre la ejecución e inspección de las uniones, con trazabilidad de los trabajos para verificar quien lo realizó.
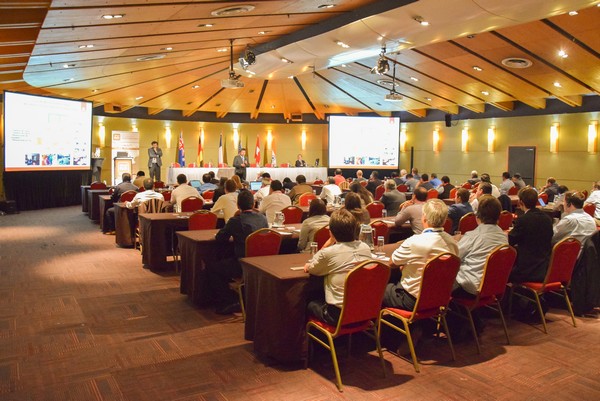
(Foto Edoctum)
Gracias a esto, se duplicó el tiempo entre fallas, lo que hizo bajar el gasto de mantenimiento de US$15 millones a sólo US$7 millones, disminuir en 30% la dotación necesaria para reparaciones, y reducir de 2 a 1 los contratos de servicios. Además, el trabajo planificado pasó de un 35% a un 75% del total. Así, el nuevo enfoque impulsó un cambio cultural en la dotación ante el objetivo común de mejoramiento continuo y productividad, según resaltó Galleguillos.
Otro ejemplo en esta línea la aportó el jefe de Planificación y Confiabilidad de las plantas SAG de El Teniente, Héctor Montanares, quien detalló el cambio de la correa 212 entre las plantas de chancado secundario y terciario, con dificultades por interferencia con nuevas instalaciones y accesos. Ello requería mes y medio de preparativos y cortes de caminos, unas 60 horas de paro de planta y reducir los empalmes y el riesgo de las personas en las maniobras de tiro. Para ello fue preciso fabricar una gran plataforma y estructuras para mover el súper-carrete con el rollo de correa de 78 toneladas y los equipos traccionadores. “Pudimos entregar la correa para el último empalme a las 36 horas de trabajo. Los preparativos no implicaron detención de correa operativa”, explicó.
La planificación detallada fue clave, lo mismo el seguimiento de los procesos de ingeniería y fabricación, y la presencia en terreno para verificar el cumplimiento del plan. “Fueron 18 mil horas de exposición a riesgos críticos y no hubo ni un solo incidente o accidente en todo el proceso, que abarca desde la fabricación, instalación y el cambio de la cinta. Fue un trabajo bien hecho y estamos orgullosos”, sostuvo Montanares.
Por su parte, Minera Los Pelambres (MLP) también logró reducir los tiempos de una reparación en una polea motriz de correa para eliminar vibraciones, cumpliendo el trabajo en sólo 75 horas en lugar de las 86 requeridas. La tarea exigió diseñar un procedimiento de desarme atendiendo los riesgos de cada fase para retirar la polea y reemplazarla.
Para que todos conocieran en detalle el trabajo, se hizo un video de 3 minutos en base a modelación computacional, el cual quedo accesible a todos los celulares. “Llegado el día ‘D’, todos sabían qué hacer y dónde. El video fue un éxito en la difusión del procedimiento para este trabajo, que hicimos en tiempo récord y cero accidentes o daños. Fue fruto de una planificación correcta, y del empoderamiento y motivación de las personas y el trabajo en equipo”, destacó Sebastián Villagra, programador de molienda Pebbles de MLP.