Chancado y molienda: Las visiones de dos profesionales especializados
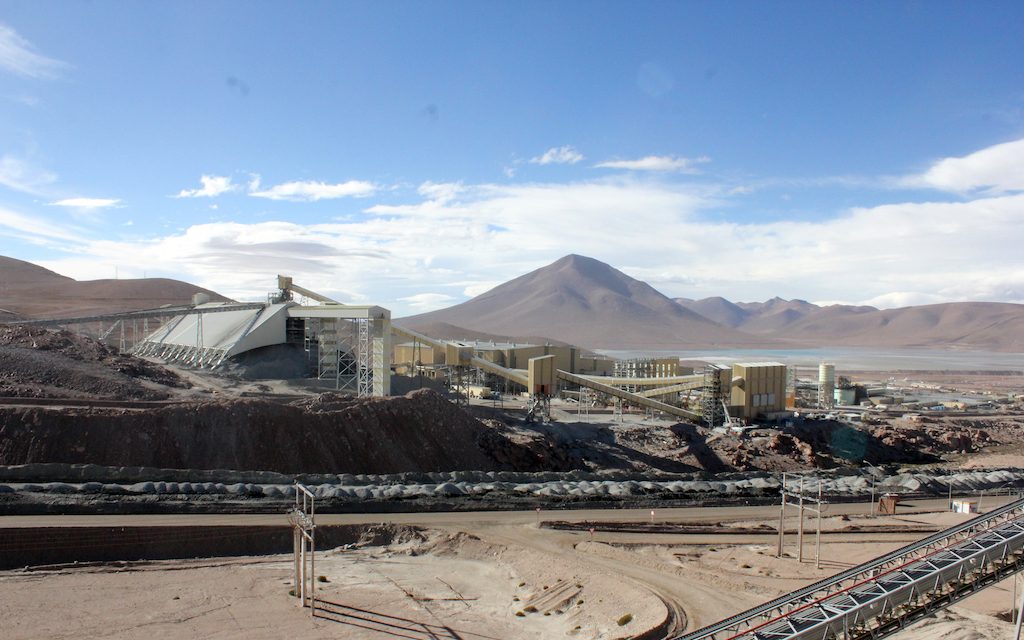
Es la etapa que concentra el mayor gasto energético y costo de toda la cadena productiva. Por ello, a lo largo de los años se han creado y aplicado distintas tendencias para optimizar los procesos de chancado y molienda. A continuación, la visión de dos expertos en el tema.
Por Daniela Tapia
Revista NME
_________________
En la minería del cobre, es sabido que son los procesos de chancado y molienda la parte de la cadena productiva que genera los mayores costos operacionales dado el alto consumo de energía, aceros de desgaste, además de repuestos y uso intensivo de mano de obra, principalmente para mantención y aseo.
Así lo señala Mario Arredondo, gerente técnico de la Consultora Industria & Minería, quien destaca que se trata de un área que debe ser utilizada eficientemente, es decir, con operadores bien entrenados, con equipos que respondan a las características del mineral, bien configurados en cuanto a número y capacidad, y con los mayores estándares de automatización y control.
Pero que para que ambos procesos impacten positivamente en la cadena productiva, deben darse ciertas condiciones. Según Arredondo, se debe tener claro que durante los 30 o más años de operación de la planta, la utilización del chancador primario no dependerá de la planta, sino siempre del número y frecuencia de camiones que envíe la mina.
Por esta razón, -dice el experto- es necesario diseñar un chancador primario aparentemente sobredimensionado y un stock pile entre el chancado primario y las siguientes etapas de conminución con una autonomía de, al menos, 12 horas. “A mi juicio, el control y operación del chancador primario debe ser realizada por la Gerencia de la Planta”, sostiene.
Agrega otro factor. “El operador de plantas sabe que chancar es más barato que moler y mejor aún sabe que mientras menor sea el tamaño de las rocas que llegan de la mina por aplicación del concepto “mine to mill”, más fácil será obtener la granulometría del producto que requiere la molienda”, añade el consultor.
Aplicando tendencias
A lo largo de los años se han creado y aplicado distintas tendencias para optimizar ambos procesos. Para el profesor en retiro de la Universidad Técnica Federico Santa María, Waldo Valderrama, destaca la preconcentración, para evitar procesar recursos de escaso valor.
“Se aumenta el rendimiento de la planta concentradora, impactando hasta la huella de carbono, aunque se genera un pasivo ambiental adicional en la disposición de este material”, explica el docente.
Sumado a ello, está la planificación geometalúrgica cuidadosa para equipos y sistemas con más instrumentación (inteligencia), lo que unido a sistemas de control más avanzados, permiten adaptarse con mayor rapidez y eficiencia a los cambios en las condiciones de proceso.
Ejemplo de esto, dice Valderrama, son las Digital Twins, sistemas de simulación de la evolución de una planta que anticipan escenarios, según posibles cursos de acción.
“Otra gran tendencia es el análisis de los cuantiosos bancos de datos que se están generando continuamente en las grandes plantas. Esto permite un estudio sumamente pragmático del comportamiento de variables en planta, con ayuda de herramientas de inteligencia artificial, donde destacan los modelos con redes neuronales, el análisis estadístico automatizado, y en general, el aprendizaje de máquina”, enfatiza el especialista universitario.
En tanto, el ejecutivo de la Consultora Industria & Minería plantea que en términos de costos de operación y del real entendimiento del proceso de conminución, el uso de los chancadores de rodillos tipo HPGR, que han sido utilizados en proyectos de Perú y considerado en varios proyectos de expansión en Chile, ha sido la nueva oportunidad o “innovación” en la última década.
“También está la externalización de los servicios de mantenimiento. Sin embargo, en los últimos cinco años se vuelven a internalizar algunos servicios clave, apuntando a la productividad y estabilidad laboral del personal esencial”, manifiesta Arredondo.
¿Qué se proyecta para este mercado?
Hoy, ante la racha alcista que ha experimentado el precio del cobre y el momento auspicioso que vive la minería, cabe preguntarse entonces por las proyecciones estimadas para el mercado del chancado y molienda.
De acuerdo a Waldo Valderrama, el desafío es gigantesco, ya que a medida que los minerales presentan menores leyes, las minas continúan siendo más profundas y más caras, por lo que mayor es la demanda de chancado y molienda para producir la misma cantidad de producto final.
“Por ello, creo que ante el alza de costo que ello implica, se crea demanda por nuevas tecnologías que pueden reestructurar este mercado”, dice el académico.
Por otra parte, Mario Arredondo sostiene que es necesario volver a las bases (back to the basis). “En este sentido, considero que se deben relevar algunos de los principios básicos del chancado y molienda, entre los cuales está controlar el setting de los chancadores todos los turnos; ocupar el agua donde corresponde (alimentación a ciclones) y no diluir a la entrada de la flotación, entre otros aspectos”, concluye el experto a modo de consejos.
¿Qué nuevas tecnologías han desarrollado las empresas vinculadas a este mercado? En las siguientes páginas, Revista NME revisa algunas de las soluciones más destacadas que se han puesto a disposición de la industria minera y que esperan marcar diferencia en materia de productividad.
Sandvik
¿Qué tecnología(s) destaca dentro del pool de equipos vinculados a chancado y molienda que tiene la compañía? ¿Cuál es su principal innovación y de qué manera marca la diferencia en la industria?
La nueva serie de trituradoras de cono premium Sandvik 800i presenta actualizaciones mecánicas, conectividad, automatización avanzada para predecir el rendimiento, maximizar el tiempo de actividad y ofrecer lo mejor en sustentabilidad al menor costo posible.
Todas las trituradoras 800i vienen con la nueva generación de sistema de control ACS y están conectadas a nuestra herramienta digital SAM. Esto permite a los gerentes y operadores acceder y administrar toda la información vital que necesitan para tomar decisiones informadas. Se puede acceder a SAM, usando una tableta o computadora.
¿Qué perspectivas proyectan para este mercado y cómo su empresa va a responder a dichos desafíos?
Actualmente estamos trabajando en la digitalización de nuestros trituradores. Los equipos conectados permiten la recopilación de datos. El verdadero valor para el cliente se crea cuando las capacidades digitales y las competencias de las personas se combinan para proporcionar análisis y soporte de servicio.
En esta línea, nuestra oferta de servicios en sitio se complementa perfectamente con nuestra oferta digital de trituración y cribado, para proporcionarles a nuestros clientes conocimientos en tiempo real basados en el IoT y modelos de aprendizaje automático aplicados.
FLSmidth
¿Qué tecnología(s) destaca dentro del pool de equipos vinculados a chancado y molienda que tiene la compañía? ¿Cuál es su principal innovación y de qué manera marca la diferencia en la industria?
FLSmidth cuenta con el chancador giratorio de quinta generación 100% Top Service, único en su categoría en el mercado a nivel mundial.
Este equipo, dentro de sus principales características diferenciadoras, considera la realización del proceso de montaje y desmontaje de sus componentes desde su parte superior, eliminando la necesidad de contar con un carro de excéntrica.
Desde el punto de vista de la seguridad, elimina la necesidad de trabajar desde la parte inferior del chancador, reduciendo la exposición a riesgos de caída, elimina el trabajo en espacios reducidos o confinados y reduce los tiempos de mantenimiento hasta en 70%, comparado con los equipos que no son completamente Top Service.
¿Qué perspectivas proyectan para este mercado y cómo su empresa va a responder a dichos desafíos?
La producción minera regional ya está dando claros indicios de recuperación, impulsado por el aumento del precio de los commodities y una franca optimización de los costos de producción. FLSmidth está enfocado en continuar siendo un socio estratégico para nuestros clientes y el proveedor número uno en productividad sustentable.
También estamos enfocados en el desarrollo de tecnologías seguras que optimicen los tiempos de mantenimiento.
Metso Outotec
¿Qué tecnología(s) destaca dentro del pool de equipos vinculados a chancado y molienda que tiene la compañía? ¿Cuál es su principal innovación y de qué manera marca la diferencia en la industria?
Dentro de nuestras tecnologías destacadas en materia de chancadores contamos con los Chancadores de Cono MP, utilizados para chancado secundario/terciario y chancado de pebbles para mineras grandes.
Dada su confiabilidad y robustez, los chancadores MP han sido la primera elección de la mayoría de las empresas de la gran minería. Ahora la familia MP incluye MP2500, el chancador de cono más grande del mundo, que puede procesar hasta 5000 tph (Check) en una línea.
En materia de molienda destacan nuestros rodillos de alta presión HRC, y a nivel de molinos SAG/Bolas, Metso Outotec ha sido pionero en implementar los tamaños de molinos más grandes mediante décadas (36’, 38’, 40’, 42’).
¿Qué perspectivas proyectan para este mercado y cómo su empresa va a responder a dichos desafíos?
Menor ley de cabeza en los nuevos proyectos, y también en las mineras antiguas, cuando la excavación avanza, por tanto, existe una necesidad de procesar mayores volúmenes de mineral para poder producir la misma cantidad de metal fino.
Equipos de gran capacidad, como el Superior 60110 Mk III, MP2500, HRC3000, VTM-4500 y el HIG-6500, reducen la cantidad de líneas de producción y reducen Capex y Opex por economía de escala.
Weir Minerals
¿Qué tecnología(s) destaca dentro del pool de equipos vinculados a chancado y molienda que tiene la compañía? ¿Cuál es su principal innovación y de qué manera marca la diferencia en la industria?
Dentro del portafolio de equipos de conminución, Weir Minerals posee la tecnología HPGR Enduron®, la cual permite un ahorro energético de hasta -40%, sin utilización de agua, disminuyendo costos operativos por consumo de elementos de molienda y logrando una disminución en la emisión de miles de toneladas anuales de CO2, es decir, un menor costo total de propiedad.
Cabe destacar que Weir Minerals posee los equipos HPGR más grandes del mundo con tonelajes sobre las 4.000T/h por equipo, lo cual impacta en la reducción del Capex de los proyectos, en la optimización del layout de la planta y los procesos posteriores a la conminución.
¿Qué perspectivas proyectan para este mercado y cómo su empresa va a responder a dichos desafíos?
A nivel global todos los indicadores muestran una base sólida sobre la cual se sustenta la demanda de los principales productos de exportación en Chile y los demás países de la región.
En ese sentido, Weir Minerals está permanentemente vinculado a la actualización de los diferentes procesos mineros de sus clientes, aportando directamente a través del estudio sus centros de pilotajes y del desarrollo de tecnologías, con foco en la disminución del consumo de agua, la eficiencia energética y la digitalización y remotización de operaciones.