Automatización: Rompiendo paradigmas en la minería chilena
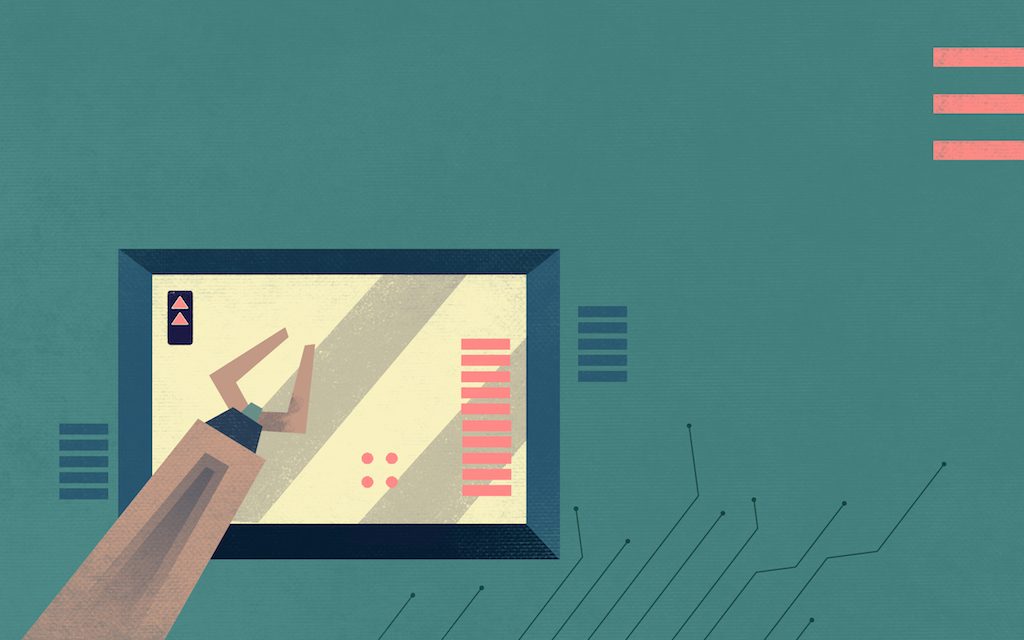
En las siguientes páginas, Revista NME repasa las iniciativas que han implementado distintas compañías mineras en materia de automatización, una apuesta que le ha cambiado el rostro a la principal actividad económica del país.
Por Daniela Tapia
Revista NME
_________________
En conjunto con el World Economic Forum (WEF), la multinacional de servicios profesionales Accenture, publicó un impactante estudio, el cual reveló que los Centros Operativos Remotos (ROC’s, por su sigla en inglés) pueden aportar unos US$65 mil millones de valor a la industria minera mundial, suponiendo una tasa de adopción de 50% a 2025.
Chile no está lejos de llegar a esta meta de adopción, estimándose que un 38% de las operaciones de las cinco principales mineras presentes en el país, ya tiene un centro operativo o en proyecto.
Hacia esta tendencia está avanzando el país, según destaca Martín Tavil, director ejecutivo para la Industria Minera de Accenture Chile. Y es que estas instalaciones son consideradas como un verdadero “cerebro”, donde se registra y analiza información fidedigna y online de los procesos mineros, logrando de esta forma una visión en tiempo real de la operación en su conjunto.
La transformación digital, en este contexto, llegó para quedarse, modificando los procedimientos de todas las industrias, especialmente de la minería. Y la pandemia del Covid-19 no hizo más que acelerar dicho cambio, donde la adopción de la automatización e inteligencia artificial resultan fundamentales, según el consenso de especialistas y actores del rubro.
“El Covid-19 ha sido clave para visibilizar este cambio en la forma de hacer minería, apresurando el proceso de implementar la automatización. Aunque ya desde hace algunos años que las empresas proveedoras están ofreciendo tecnologías para las operaciones y eso actualmente está entregando resultados palpables”, sostiene Carlos Valencia, gerente de Automatización Epiroc Chile.
Por su parte, el vicepresidente de la Región Andina y Cono Sur de Sandvik Mining and Rock Technology, Patricio Apablaza, plantea que muchas empresas mineras han estado trabajando durante años para avanzar en la digitalización de sus operaciones, pero la incorporación de nuevas tecnologías significa cambiar fundamentalmente la forma en que se ejecuta la operación.
“El mayor desafío es saber exactamente qué se pretende lograr con este proceso y dónde quieren los gerentes que estén sus minas en el futuro, por lo cual el proceso de gestión de cambio y gestión de riesgos de seguridad serán claves para el éxito en la adopción de las nuevas tecnologías”, dice.
Desde el punto de vista tecnológico, Apablaza añade que uno de los retos más importantes para los proveedores de estas tecnologías, es lograr que su oferta digital de “sistemas para equipos y funciones autónomas, sistemas para la gestión y optimización de procesos y soluciones de análisis de datos” se integren dentro del ecosistema digital más amplio en cada uno de los sitios de sus clientes.
En Accenture Chile también relevan la importancia que ha ido adquiriendo la automatización en la industria minera, lo que se ratifica en otro estudio realizado por la entidad en conjunto con País Digital.
De acuerdo al reporte, si es que la industria minera chilena invierte de forma estratégica en nuevas tecnologías y prepara a las personas para trabajar de forma conjunta con estas nuevas tecnologías, se podrían agregar US$2,8 mil millones al PIB de Chile hacia el año 2030.
Expectativas favorables
Para Carlos Valencia, de Epiroc Chile, el escenario que se proyecta es alentador. En su opinión, vamos a ver una minería que buscará llegar a un 100% de ciclos automatizados, no así de operaciones autónomas.
El ejecutivo describe su punto de vista, argumentando que no es posible pensar en que todo el proceso minero se desarrollará de forma autónoma.
“Por ejemplo, podemos tener mallas de perforación que sean 100% autónomas, pero se deben dar las condiciones para eso. En general, hablamos de una combinación donde el 80% de la malla puede ser full automatizada, mientras que el 20% restante necesita la intervención de operadores en forma teleremota, ya que hay pozos que se perforan de forma especial”, detalla el especialista de la firma proveedora, quien cree que la incorporación de tecnología marcará esta nueva era de la minería y le dará un gran impulso.
En tanto, el experto de Accenture Chile manifiesta que el panorama que viene es de una aceleración total de la automatización y de adopción de nuevas tecnologías, donde la minería se posiciona entre las industrias que más han proyectado inversiones en nuevas tecnologías para este 2021.
“Así, por ejemplo, la nueva tecnología en la que más invertirán los ejecutivos del sector a nivel global es Internet de las Cosas/sensores inteligentes, con un 95%; en inteligencia artificial, 89%; y en robótica, un 88%”, explica Martín Tavil.
¿Qué soluciones ha implementado el sector minero chileno en el campo de la automatización? En las siguientes páginas, Revista Nueva Minería y Energía revisa las principales iniciativas que han aplicado distintas compañías mineras en esta materia, una apuesta que le ha cambiado el rostro a la actividad económica más significativa del país.
Manejando Los Bronces desde Santiago
El Centro Integrado de Operación Remota o IROC, por su sigla en inglés, es la primera instalación en su tipo en el mundo de Anglo American y permite controlar la mina Los Bronces en tiempo real y en forma integrada desde las oficinas corporativas en Santiago, transformándose así en el cerebro de la operación y en donde se materializan todos los proyectos de digitalización y de tecnología de control remoto.
Específicamente, en Anglo American cuentan que el IROC opera desde el piso 48 de la Torre Titanium, incorporando tecnologías de inteligencia artificial y rutinas de trabajo que permiten la búsqueda de un óptimo global, a través de un modelo digital de la mina, con el cual se puede monitorear el cumplimiento del plan semanal de mina en línea.
Además, se pueden observar los procesos de Geomecánica, Perforación, Carguío y Transporte, Servicios Mina, Chancado, Molienda, Flotación, Sistema de Transporte de Pulpa, Planta de Cátodos; y contempla áreas de apoyo a la operación, como mantención a través del monitoreo de condiciones de equipos de mina y planta, logística de suministros y productos, equipos de planificación mina y metalurgia.
“En el IROC se desempeñan más de 100 personas en un sistema de turnos y de ellas, más de un 80% son operadores que antes debían subir a faena, disminuyendo los tiempos de traslado y la exposición a las condiciones naturales y extremas de Los Bronces”, comentan desde la compañía.
El espacio, además, cuenta con 32 estaciones de trabajo que reciben la información proveniente de la faena, donde están instaladas más de 700 cámaras que capturan los distintos procesos que tiene la mina, para extraer y procesar los minerales.
“Estas imágenes, y la información que se obtiene, se transmiten por conexiones de fibra óptica para mantener la seguridad de la comunicación, hasta la oficina remota donde se distribuyen en 150 pantallas de última generación, un videowall con 50 servidores, y distintos sistemas computacionales que sirven para analizar datos y procesos”, añaden en la minera.
BHP, con foco en la autonomía y la mejora continua
BHP está impulsando en Chile el programa Copper Material Handling (CMH) que considera la ejecución de proyectos de manejo de materiales mina, “a través de soluciones innovadoras y disruptivas que desafíen la forma en que trabajamos y contribuyan a resolver los retos que enfrentan las operaciones”, señala la propia compañía.
CMH tiene dos proyectos asociados: Escondida Material Handling (EMH) y Spence Material Handling (SMH). Ambas iniciativas están estudiando soluciones para el manejo y transporte de materiales en la mina a través de la introducción de autonomía y cambios en las fuentes de abastecimiento de energía para el movimiento de los camiones y correas transportadoras.
Actualmente se encuentra operando un piloto de camiones autónomos en Escondida. De manera paralela, tanto Escondida como Spence están transitando hacia el uso de perforadoras autónomas.
En el caso de la primera, ya se encuentran dos perforadoras autónomas en operación. En el caso de Spence, prontamente llegarán los nuevos equipos.
Otra apuesta relevante de la firma minera es el Centro de Operaciones Integradas (CIO, por su sigla en inglés), el cual funciona en las oficinas de BHP en Santiago desde julio de 2019.
“Los especialistas del CIO operan desde estas oficinas corporativas todas las áreas de control de los procesos de producción de Spence y Escondida”, dicen en BHP.
De esta manera, el CIO permite la integración de las áreas productivas en tiempo real, permitiendo la optimización de procesos a lo largo de la cadena de valor en forma integrada.
“Además, gracias a este centro es posible alcanzar una mayor estabilidad operacional al tomar decisiones de una manera holística, a lo que se suma que la visibilidad y administración de la información, facilita y fomenta procesos de mejora continua a través de dinámicas avanzadas de Data Analitics y Machine Learning, entre otros”, agregan en BHP.
Teck dispone de tecnología de vanguardia para Quebrada Blanca
El proyecto Quebrada Blanca Fase 2 (QB2) de Teck será una de las operaciones de cobre más grandes del mundo, la cual se desarrollará bajo el actual yacimiento de la operación Quebrada Blanca.
Para apoyar su tamaño y alcance, la canadiense Teck destaca el Centro de Operaciones Integradas, un núcleo de inteligencia que optimizará los procesos y las operaciones, inspirado en la Minería 4.0 que se centra en el uso de la tecnología inteligente para racionalizar, automatizar y mejorar las prácticas mineras convencionales.
Ubicado en la ciudad de Santiago, el Centro de Operaciones Integradas de Teck operará completamente la cadena de producción de Quebrada Blanca, centralizando los recursos y los datos para la toma de decisiones y optimización del desempeño.
“Todo esto se logra sin barreras geográficas, a través de un amplio soporte de conectividad y control de procesos integrado, desde la mina hasta el puerto, que obtendrá datos operacionales en tiempo real desde el yacimiento, situado en la región de Tarapacá a 4.400 metros sobre el nivel del mar y a 1.700 kilómetros de distancia de la capital”, indican en Teck.
La automatización al centro de El Teniente
Desde la División El Teniente de Codelco apuestan por la tecnología para el futuro de su mina subterránea, la que cuenta con palas LHD y camiones automatizados que serán fundamentales para consolidar una operación más segura y productiva.
Los equipos LHD en las minas Esmeralda y Diablo Regimiento realizan el traslado y vaciado del mineral en forma autónoma, con un operador/a que realiza la tarea de carguío desde el Centro Integrado de Operaciones (CIO) de Rancagua, ubicado a unos 80 kilómetros de la faena.
“Bajo la misma directriz ejecutiva de El Teniente, los proyectos Diamante, Andesita y Andes Norte trabajan en el modelo operacional con equipos LHD y camiones autónomos. Ése es el desde para la Mina, donde todos los equipos nuevos deben ser automatizados”, resalta Rodrigo Andrades, gerente de Minas.
La firma minera también destaca que la automatización de equipos permitirá recuperar sectores cerrados por riesgo de bombeo de agua barro, donde la tecnología posibilita su operación a distancia, como es el caso de algunas áreas en Diablo Regimiento y Esmeralda.